The Future of Warehouse Modernization
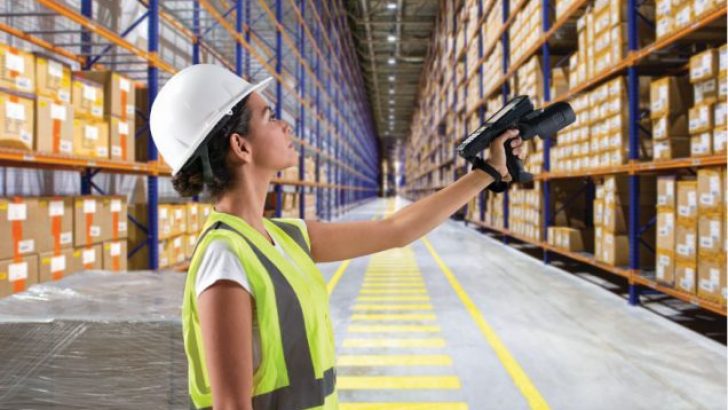
How a strategic, phased approach to warehouse automation simplifies technology deployment while accelerating productivity and cost-savings.
By Mark Wheeler, Director of Supply Chain Solutions, Zebra Technologies
In the last decade, the world of ecommerce has changed dramatically. The “acceptable” time from order to delivery has plummeted from 1-2 weeks to 1-2 days (or even hours). The number of stock keeping units (SKUs) that must be managed and sorted has skyrocketed, while the available labor pool has shrunk.
Then COVID-19 hit, and ecommerce sales grew nearly a third in just a few months.[i] Many manufacturers and warehouse operators are still struggling to keep up with the demand, particularly in light of the supply chain, inventory and fulfillment challenges caused by the pandemic.
Companies realize they need more automation and visibility in their warehouse operations to adapt to this unpredictable world. But today only 35% of warehouse operators have a clear understanding of where to start[ii] and many view the process of building an autonomous warehouse as an elephant-sized task. Following a phased, strategic approach to automation can simplify the modernization process for warehouse operators while also accelerating the return on their technology investment.
Phase 1: Improve Operations for Greater Individual Worker Productivity
The goal of the first phase is to gain control of basic business operations across all inventory processes. Start by focusing on simple solutions that increase individual worker productivity to get a quick return on investment (ROI). Introduce mobile scanning that accurately reads 1D and 2D barcodes on the first scan every time, or even multiple barcodes with a single trigger pull – even if labels are dirty, damaged or far away. Warehouse operators should also consider intuitive mobile computer or printer operating systems (OS). Today’s enterprise mobile computers operate on the Android™ OS to give users the same familiar interface as their personal devices but are rugged enough for warehousing. Thermal printers no longer require extensive training to operate, reload media, and change or update settings, removing barriers to critical inventory data.
Phase 2: Connect Workers for Greater Team Productivity and Workflow Conformity
The next step to optimizing technology investments is leveraging task-specific devices and form factors, such as wearable devices, handheld mobile computers, tablets or mobile printers, to capture data and improve visibility throughout warehouse operations. This allows warehouse leaders to adjust tasks, identify improvement areas and maximize productivity. By dynamically assigning tasks based on warehouse management system (WMS) data and contextual data from mobile devices, employees can be directed to their best-next-action based on factors such as location or order urgency. By doing so, workers are connected to each other and the WMS, onboarding time decreases, and workflows are optimized.
Phase 3: Integrate for Greater Asset Visibility and Utilization
Phase 3 introduces sensor-based data collection. In earlier phases, data capture is transactional and only gives the WMS limited glimpses of visibility into a warehouse’s physical operations. Automated data capture gives a more complete, real-time view of physical operations. For example, in the case of receiving, manual scans have missed entire cases of incoming goods. With a radio-frequency identification (RFID) system though, tagged goods are counted as soon as they pass through dock doors with a fixed RFID reader in the portal areas. Workers now manage by exception. Sensor-based data collection helps ensure increased accuracy, better asset utilization, and decreases time spent locating assets.
Phase 4: Be Responsive for Best Next-Move Guidance and Decision-Making
Now, sensor-based, real-time data capture is expanded more broadly across the entire facility. In this phase, orchestration and integration of real-time locating systems (RTLS) with the WMS and other management systems are achieved, allowing operators to automate what can automated and optimize the physical flow of products from receiving through shipping using real-time edge data. In the movement of goods, sensors automatically associate forklifts and pallets to show goods on the forklift as it travels, without the need for manual barcode scanning upon pick-up. At drop-off, the forklift and pallet are disassociated, the pallet shows as delivered and the forklift shows it is ready for its next assignment. This same scenario also applies to autonomous mobile robots (AMR) with ready-to-ship materials from picking to loading. Resources and assets are orchestrated, optimized, sequenced and directed so throughput volumes, cost and workflow speed are improved.
Phase 5: Predict and Adapt to Proactively Improve Performance
Finally, once data intelligence systems are deployed throughout the warehouse, companies can begin to use data analytics and artificial intelligence (AI) to uncover ways to improve their processes even further, whether that’s by updating their warehouse design or perhaps changing employee workflows. Companies can also use the data to quickly identify or predict changes in consumer buying habits, supplier shortages and other issues that could impact business profitability – and use that data to rapidly adapt.
The migration to the modern warehouse is accelerating, with 68% of warehouse executives reporting that they plan to focus on increasing visibility, real-time guidance and data-driven performance within the next five years[iii]. Using a phased approach to warehouse modernization allows operators to break down the automation process into manageable pieces – and quickly identify areas where technology can help improve productivity and ROI.
About Zebra Technologies:
Zebra (NASDAQ: ZBRA) empowers the front line in retail/ecommerce, manufacturing, transportation and logistics, healthcare, public sector and other industries to achieve a performance edge. With more than 10,000 partners across 100 countries, Zebra delivers industry-tailored, end-to-end solutions to enable every asset and worker to be visible, connected and fully optimized. The company’s market-leading solutions elevate the shopping experience, track and manage inventory as well as improve supply chain efficiency and patient care. In 2020, Zebra made Forbes Global 2000 list for the second consecutive year and was listed among Fast Company’s Best Companies for Innovators. For more information, visit www.zebra.com or sign up for news alerts. Participate in Zebra’s Your Edge blog, follow the company on LinkedIn, Twitter and Facebook, and check out our Story Hub: Zebra Perspectives.
Source: Mark Wheeler | industrytoday